Multi-ability unmanned aerial vehicles have grown attention in the last decade. They also provide the advantage of vertical take-off and landing and forward flight and eliminate the single flight-mode UAV configuration. Despite the multi-ability UAVs growth, the lack of efficient online transitioning mechanism is persistence. In our research, we propose an online reconfigurable UAV design optimization process.
A configuration based on a novel wing-mounted dual rotating rotor blended wing body design is proposed, which provides improvements in current transitioning UAVs performance from different aspects.
The design encompasses 4 DC motors mounted to two aluminum rotating frames, two power-off brakes and 2 servo motors to actuate the elevens as shown on Figure 1. The proposed transition mechanism is a unique two-step procedure. For hover to forward flight transition, rotors should transfer from a zero-degree angle to 90-degree angle respect to body y axis. The rotation is accomplished in two steps, first it goes from hover to a pre-defined intermediate angle and fly at that angle until it reaches the desired forward flight velocity, which is forward flight cruise speed. And then, it completes the second transition to forward flight mode.
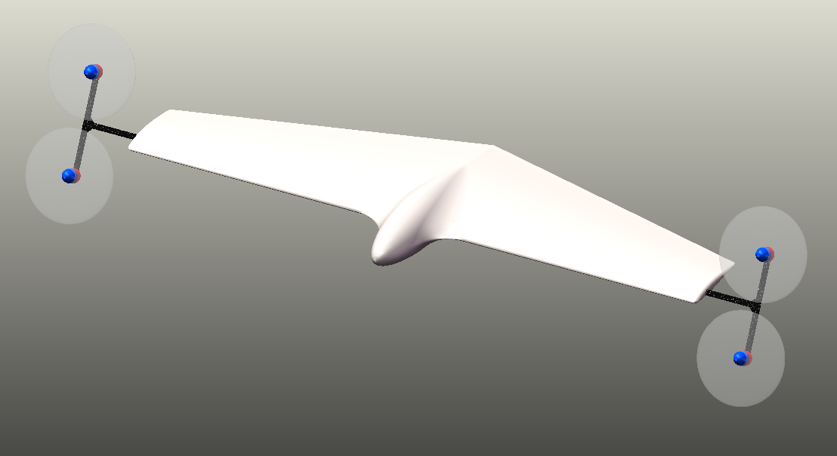
Figure 1: Blended wing body tilt rotor Configuration.
In this research, we optimize the proposed design for specific mission requirements. Scope of optimization process is shown in Figure 2.

Figure 2: Optimization scope flowchart.
In optimization process, we need to update UAV modeling outputs for each candidate design. Our model consists of three subsystems; aerodynamics, weight and moment of inertia calculation, and dynamic simulation. The aerodynamic modeling is done using low-fidelity models such as vortex lattice method and an element by element weight and inertia calculation is done for weight and moment of inertia calculation and weight balance.
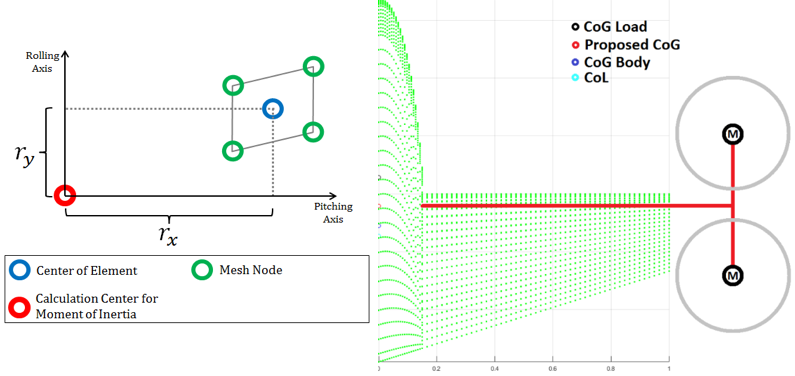
Figure 3: Element-by-element Weight & Inertia Calculation, Plus Sketch of The Power System (Single Side
For a baseline design, we analyze the proposed transition performance. In Figure 4, we can see simulation results for takeoff and transition from hover to forward flight transition performance of the UAV. We can see that transition procedure has been completed. As we can see, the first step transition is relatively slow, but second step transition is sufficiently fast and it can be accomplished in about one second. We can notice the appropriate response of angular rotation input and differential thrust for making the transition.